Improve On-time in-full Performance with Supply Chain Visibility
Over the last few decades, supply chains have become volatile and are subjected to market fluctuations, trend shifts, and unpredictable changes. Companies use different ways to measure and improve supply chain performance, one of which is an important metric: OTIF (On Time In Full). Your suppliers’ performance aligns with the outcomes you achieve, which rings especially true for OTIF.
Imagine you are a fashion brand that runs a retail store that delivers clothes to customers. You want to ensure that your customers receive their orders on time and in full, according to their preferences and specifications. However, this comes with challenges like fluctuating demand, diverse customer choices, different clothing design availability, and unpredictable traffic conditions. You must constantly monitor and analyze your order history, customer feedback, inventory levels, and delivery routes to improve your OTIF performance. You must keep innovating and experimenting with new designs, fabrics, and trends to satisfy your customers and stay ahead of the competition.
Likewise, improving the OTIF score in a supply chain will take planning and addressing the common challenges holistically.
What is Fill Rate?
A fill rate measures order fulfillment and is used to forecast inventory levels. The higher the fill rate, the better the ability to fulfill sales without stockouts, backorders, or lost sales. A low fill rate indicates that there is not enough stock on hand.
How to Calculate Fill Rate?
Fill Rate = Shipped Orders/Total no. of Orders X 100
For example, if you were to receive 200 orders and fulfill 85 of them, fill time would be calculated like this:
Fill rate = 185/200 X 100
In that situation, you would have a 92.5% fill rate.
What is OTIF?
OTIF is a pivotal supply chain metric in the logistics industry. The key metric is a barometer to measure the percentage of orders a business can deliver within the agreed lead time and at the expected volumes (i.e., no missing goods). Organizations use OTIF to benchmark and compare supplier performance, enabling them to make better procurement decisions.
Why OTIF Matters?
Every business wants a 100% OTIF rate, meaning all deliveries are on time and in full. However, 95% or more is rated as an excellent OTIF benchmark, signifying that 95 out of 100 deliveries were in full volume at a promised timeline. The stakes are high for suppliers who do not adhere to OTIF standards – from lost revenue opportunities to hampered relationships. Let’s understand the practical OTIF meaning through Walmart, a leading retailer that often fines suppliers who fail to meet OTIF practices. Walmart levies a penalty to shippers of 3% of the cost of goods sold for delayed and incomplete deliveries. 28% of companies surveyed experienced inventory shortages and looked for alternate sources of supply. Suppliers with real-time visibility into their operations and optimized transportation can avoid such repercussions.
Retailers cannot afford to lose customers due to empty shelves and delayed shipments, while manufacturers and distributors are also at risk of losing relationships with retailers due to incomplete orders or late deliveries that may necessitate expedited shipping ways; that’s when optimizing OTIF metrics becomes essential. Meeting delivery timeframes and ensuring all ordered products are available and delivered as retailers expect are crucial to achieving supply chain excellence in today’s competitive market. End-to-end visibility into supply chain operations can help suppliers reduce logistics costs, beat the odds, and stay financially viable.
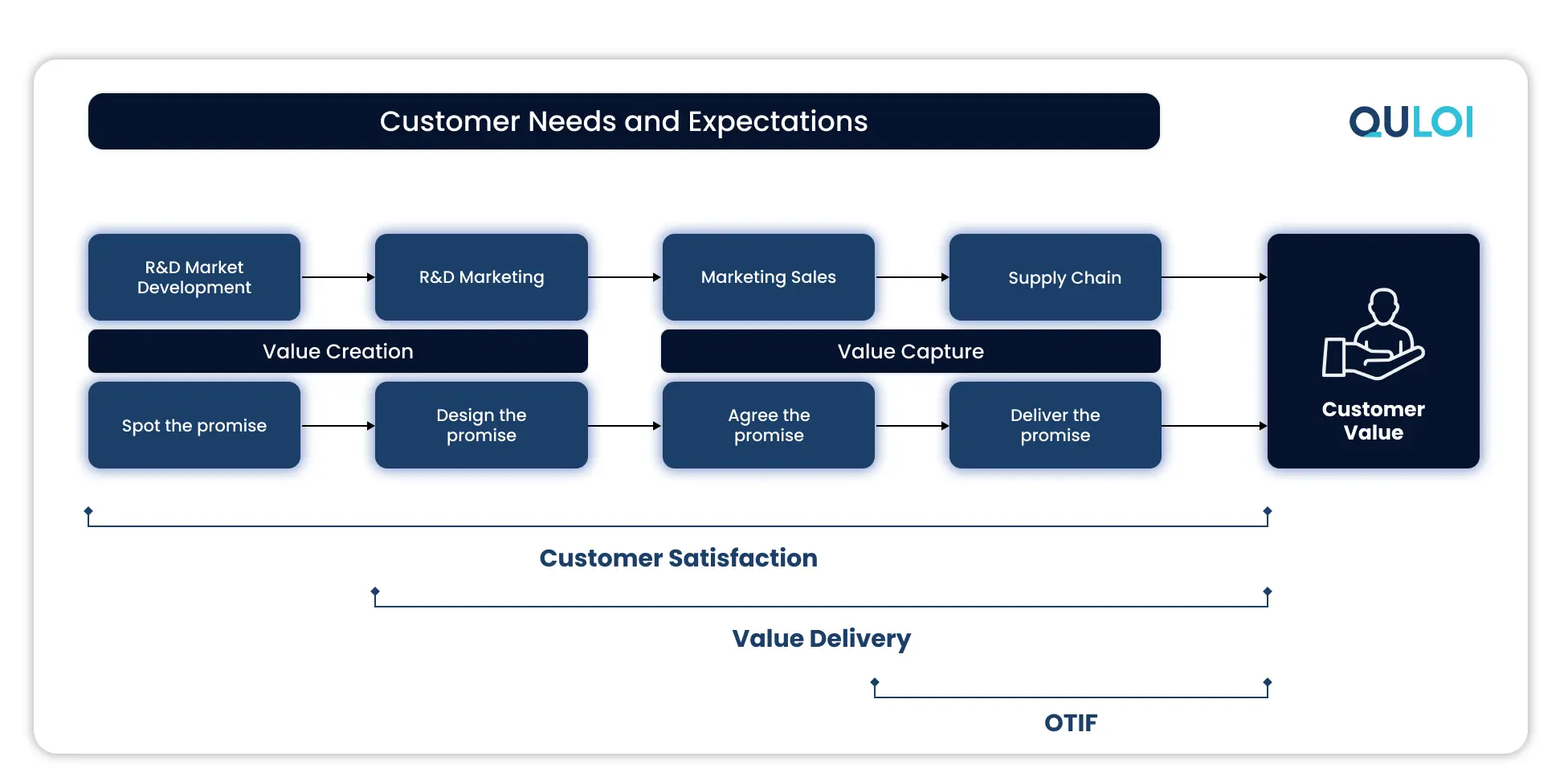
Measuring OTIF
The phrase ‘If you can’t measure it, you can’t manage it.’ can be attributed to supply chain management. The phrase frequently used, ‘If you can’t measure it, you can’t manage it.’ can be attributed to supply chain management. To improve your supply chain performance, you must measure it. There is no fixed industry practice to calculate OTIF; however, the standard way to calculate it is as follows:
OTIF = Number of deliveries on time, in full X 100
Total no. of deliveries
For Example, A furniture company has 200 beds to deliver and delivers 190 on time and in full. The OTIF score would be measured as follows:
OTIF = (Number of Beds Delivered On Time and In Full / Total Number of Beds) x 100
OTIF = (190/200) x 100
OTIF = 95%
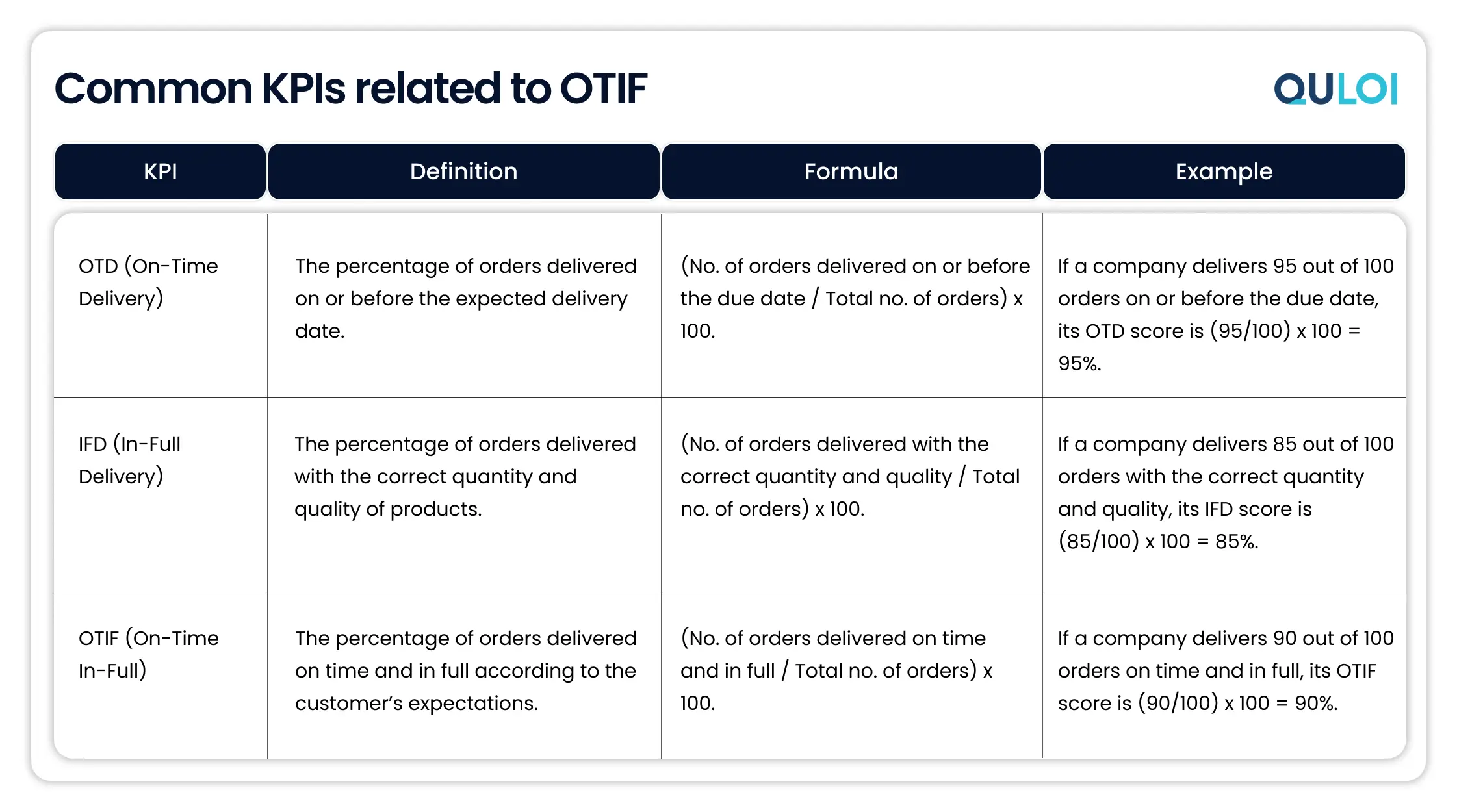
Key Challenges in Achieving High OTIF Rates
Nothing hinders supply chain performance more than a low OTIF score. It can be challenging to achieve high OTIF scores when common challenges interrupt the operations. Some of these include:
Poor Visibility
As organizations gear up to fulfill their end-to-end potential, a lack of visibility throughout the supply chain poses a barrier to promptly identifying issues and implementing preventive actions. According to a report, 57% of business leaders recognize that greater transparency and control over supply chains are needed to minimize disruption-related costs and maintain operational efficiencies.
Inadequate Technology
Outdated technology and tools can slow down order processing and impede real-time tracking and reporting. Using obsolete technology means staying behind the competition due to insufficient or incorrect information for decision-making, often resulting in inefficiencies.
Ineffective Collaboration
Using fragmented systems impedes seamless collaboration, giving rise to gaps in the organizational structure. Communication breakdowns can result in stagnant or late deliveries, increased labor costs, and mismanaged inventory – ultimately deterring the success of a group working together on a project. Such issues, if left unaddressed, can affect OTIF performance and cause disputes or penalties.
Transportation and Logistics
According to 70% of the companies, speed and accurate estimated times of delivery (ETD) are currently their key challenges. Weather conditions, carrier performance, mechanical failures, traffic congestion, etc., and other factors can severely impact OTIF performance and result in delivery delays or failures.
Paving a Way Towards Your Supply Chain for OTIF Excellence
Implementing Cross-Functional Visibility Tools
With fluctuating capacity and demand for faster delivery times, cross-functional visibility is required to maintain schedules and improve collaboration. A supply chain visibility solution enables cross-functional coordination by integrating data from diverse sources and systems, such as ERP, IoT, etc.
Digital Platforms for Real-Time Communication and Data Sharing
A cloud-driven platform connects supply chain stakeholders, such as manufacturers, retailers, suppliers, distributors, and customers. It enables data sharing and real-time communication within teams, departments, or organizations by facilitating information exchange, document sharing, contract management, order management, workflow management, etc. The centralized platform supports visibility, traceability, compliance, and supplier collaboration. 63% of manufacturers prioritizing supply chain collaboration reported on-time delivery rates of over 95%.
Leveraging Technology for Real-Time Supply Chain Monitoring
A Gartner study predicts that through 2024, 50% of supply chain organizations will invest in applications that support artificial intelligence and advanced analytics capabilities. Leveraging technology will dismantle old-school hierarchies and data management processes, identify potential OTIF issues, and help organizations automate their tasks for better operational efficiency.
Tracking Inventory and Order Fulfillment with Enhanced Visibility
In 2022, eCommerce sellers lost almost $2 trillion to issues related to mismanaged inventory. A poorly managed inventory means a substantial financial loss. Supply chain organizations must optimize inventory to prevent a domino effect or a cascading breakdown. Enhanced visibility can lead to better inventory management, eliminating unnecessary costs.
Data Analytics
According to McKinsey, most employees will use data to optimize nearly every aspect of their work by 2025. McKinsey also suggests that data-driven enterprises will have five key characteristics: agile, scalable, resilient, customer-centric, and innovative. Using data analytics, decision-makers can proactively ensure supply chains remain robust and responsive. Supply chain digitization offers valuable insights into operations for real-time decision-making.
Effective Communication Strategies for Improved OTIF Performance
A Comprehensive Supplier Scorecard captures data through OTIF performance metrics and enables procurement teams to monitor if suppliers perform their role and meet buyers’ expectations. A scorecard enables effective communication by facilitating clear and consistent measurement of OTIF expectations, improvement goals, etc.
Wrapping Up
Improving the OTIF rate is a continuous ongoing process that requires constant monitoring, evaluation, and improvement of the performance metrics and willingness to adapt to changing customer needs and market trends. By identifying the root causes of low OTIF rates, it is imperative to leverage technology, integrate visibility and collaboration into the supply chain, and evaluate supplier performance to achieve faster and more reliable delivery performance, increased customer satisfaction, and competitive advantage in the industry.
In addition to improved OTIF, Quloi – a digital supply chain visibility platform, brings direct and indirect benefits to supply chain operations. If you want to learn how Quloi helps you improve your OTIF score, contact our experts or book a demo.
FAQ
What does OTIF mean in supply chain?
On Time In Full (OTIF) is a crucial metric to measure suppliers’ delivery performance by evaluating whether they deliver orders on time and in full. Achieving a high OTIf score determines efficiency and reliability in the supply chain process.
How is OTIF calculated?
Organizations can calculate OTIF by dividing the number of deliveries made on time and in full by the total number of deliveries, then multiplying by 100. It is usually calculated as a percentage.
What is On Time And In Full (OTIF)?
OTIF is a supply chain KPI that evaluates a supplier’s capacity to meet its order delivery commitments. It measures the supplier’s ability to ship orders in the requested quantities, at the right place, and on a specified schedule. Most organizations employ the OTIF KPI, which provides businesses with a comprehensive overview of the quality of their logistics service.
OTIF Formula
OTIF Forumla = Number of orders delivered on time, in full/Total no. of orders delivered X 100
How to improve OTIF in supply chain?
There are multiple ways of improving OTIF performance in supply chain, including:
- Invest in real-time tracking systems for enhanced visibility.
- Monitor performance by establishing KPIs and tracking them regularly.
- Use demand forecasting for efficient stock management.
- Identify and eliminate bottlenecks with streamlined operations.
- Collaborate with suppliers: Improve lead times and reliability with supplier collaboration.
- Evaluate routes and carriers for efficiency through optimized transportation.