The Impact of First-Mile Inefficiencies on Last-Mile Delivery
Overview of First-Mile Delivery
The initial stage of the supply chain, where products/goods are sent from the manufacturer to warehouses, is known as first-mile delivery. This stage must be handled with care and precision as it impacts the success of middle-mile and last-mile deliveries.
Manufacturing facilities witness thousands of products being produced daily. However, these goods must reach their final destination by navigating complex logistics. It would not be wrong to call first-mile deliveries the “Hero of The Supply Chain.” The reason? It defines the overall effectiveness of the delivery process.
However, each stage of the supply chain has challenges and benefits. These parameters can lead to sleepless nights for managers if they do not make an effort to optimize operations and cater to customers’ diverse demands. Let us discuss the key challenges in first-mile delivery, its importance, and what actions can be taken to improve first-mile efficiency in the supply chain.
First-Mile Delivery Challenges
1. Order Processing Delays: With a slew of rapid delivery options available, consumers value same-day delivery. A survey by Shipedge found that poor visibility in first-mile operations strongly influences last-mile performance. Ineffective tracking of freight flow from a warehouse to a hub results in last-mile delivery delays, impacting customer satisfaction. Manual order processing or inventory inaccuracies significantly impact delivery times. According to research, 44% of consumers report that up to 10% of their orders arrive later than expected, and another 20% experience delivery delays for up to 25%. This highlights a pressing concern for improved shipping reliability in the supply chain.
2. Transportation Issues: Urban areas often face traffic congestion, leading to delays in the transportation of goods. A recent report highlighted the time and expenses wasted on transportation. US traffic congestion cost over $70.4 billion in 2023, a 15% boost from 2022. Thai indicates an average driver lost 42 hours to traffic congestion – almost wasting a whole work week. Further, the shortage of drivers exacerbates delivery challenges. In 2023, the American Trucking Association reported a significant shortfall of about 80,000 drivers. Reduced capacity of drivers can lead to order backlogs and long waiting times for customers.
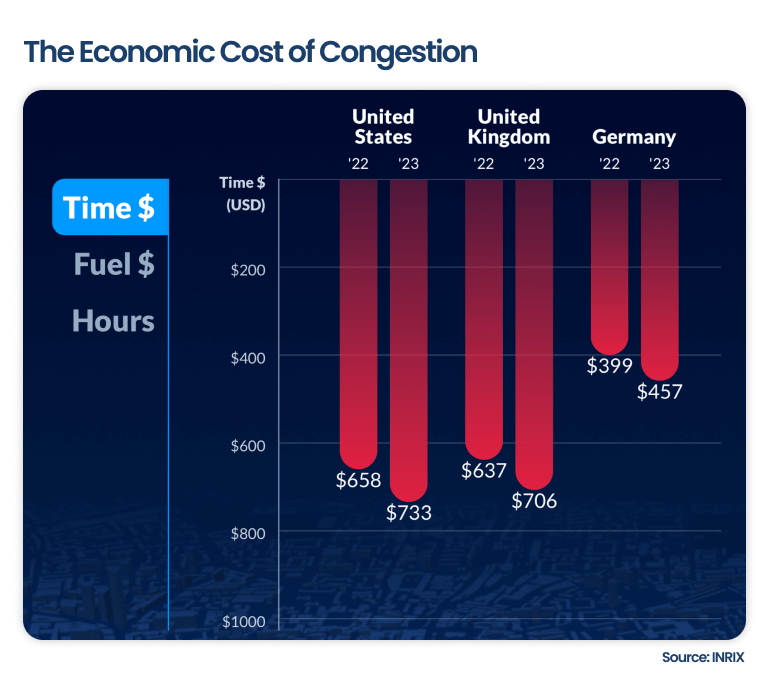
3. Inventory Management Problems: When a company overestimates its inventory, it may delay order placement, resulting in stock shortages. Conversely, companies might rush to place urgent orders if they underestimate inventory, causing delays in first-mile delivery as suppliers rush to fulfill last-minute requests. An IHL research project projected that the cost of inventory distortion – stemming from excess and out-of-stock situations – will reach a staggering $1.77 trillion for retailers globally in 2023.
4. Role of Supplier Reliability: Some suppliers may have long lead times but offer cost-effective services, whereas reliable suppliers with quick response capabilities may charge high. Choosing a cheaper, less reliable supplier can help a firm minimize its inventory cost but will also expose itself to potential risks. Furthermore, poor communication between suppliers and logistics providers can lead to misunderstandings, inconsistent quality, and timeliness.
Importance of Last-Mile Delivery
Last-mile deliveries can make or break your logistics chain. You must ensure the products/services reach the recipients immediately. With last-mile deliveries slated to increase by 78% in 2030, it is time to assess costs and optimize them to improve your business. Here are some challenges that you need to overcome in the long run.
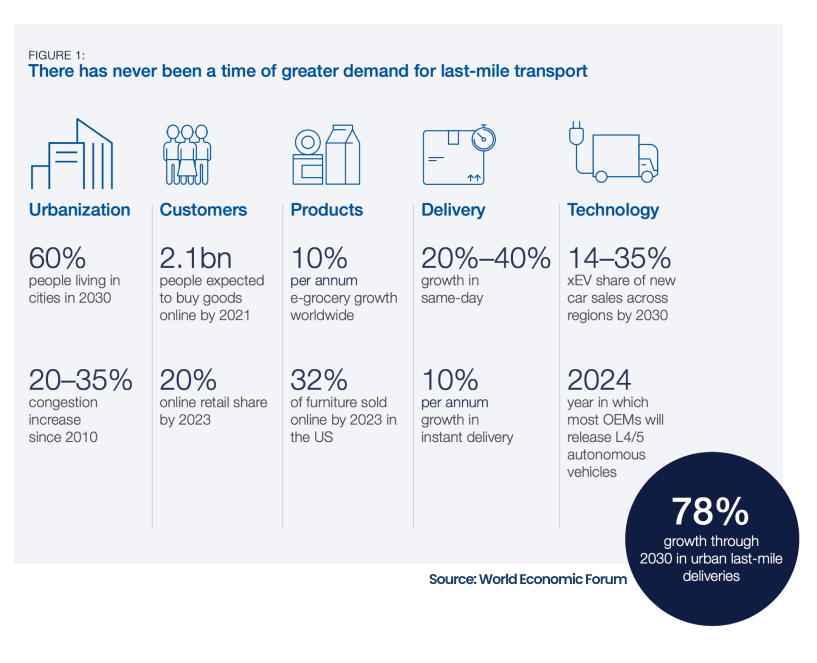
1. Higher Costs: Gone are the days when finding addresses in urban and remote areas was easy. With GPS giving false results, non-reliance on human inputs, and confusing locations, you will soon burn a hole in your pocket if you are not optimizing your supply chain. You must manage multiple vehicles and drivers while ensuring they can leverage technology and are well-versed in the area to aid timely deliveries. Not doing so will increase cases of returns and add to losses.
2. Traffic and Congestion: Optimized routes and scheduling come in handy when orders have been placed well in advance. However, festivals, maintenance of roads, and unexplained incidents can lead to difficulties and late deliveries. This can lead to poor customer ratings and even client loss (in some cases)
3. Environmental Impact: Last-mile deliveries are responsible for increased pollution and carbon emissions. In some instances, vehicles have not gone to pollution checks for longer and rely on traditional fuel methods. This negatively impacts air quality and the environment in the long run. According to the World Economic Forum, urban last-mile delivery emissions will likely increase by over 32% by 2030.
4. Last-Minute Changes: Demand for last-minute changes and flexible delivery options can add to operational issues for your business. Not only will costs rise, but it can also lead to frustration in managers, employees, and your delivery partner. Thus, to keep costs in check, you must cap your customers’ flexibility.
The Link Between First-Mile and Last-Mile Delivery
The first and last-mile delivery processes are interdependent. Each stage has a pivotal impact on the other. Here is how they influence each other.
1. Accurate Sorting and Pickups: Inaccurate sorting in the first stage can lead to misdeliveries or delays in the last mile. At the same time, if there is a lag in the first-mile pickup, there are minuscule chances of delivering products/services on time in the last stage.
2. Improper Packaging: According to Catalpa, 74% of consumers claimed that transparency and honesty in product labeling help them gain trust in the brand. If the packaging and labeling are not up to the mark in the first mile, it can lead to loss or damage during the last-mile delivery. The losses due to tampered or spoilt items can be heavy. Thus, it must be packaged according to their shape, size, and materials to ensure seamless delivery and maintain customer trust.
3. Lack of Real-Time Feedback: Companies are often skeptical of implementing technology to handle first—and last-mile deliveries. This can lead to delayed issue resolutions and dissatisfied customers.
4. Increased Costs: Inefficiencies like rerouting and rehandling are common in last-mile deliveries. However, their source continues to be the same: first-mile deliveries. If goods are sourced from micro-warehouses and handled effectively, you can cut the errors right in the first stage and prevent losses.
5. Reduced Capacity: If packages are not sorted and monitored in real-time in the first stage, there is added pressure on the last-mile delivery resources. If a warehouse manages higher volumes of packages as per its capacity, there are higher chances of error in the last mile.
6. Poor Visibility: If you cannot track goods in the first stage, you have set the stage for delays. This means if goods have not been procured, sorted, and packed well and you have zero knowledge about them, it will lead to multiple confusions. With customers wanting real-time updates, you will lose out to your competitors.
Once you understand the nuances of first—and last-mile deliveries, you can adopt a balanced approach and significantly boost efficiency.
Strategies to Improve First-Mile Efficiency
Improving first-mile efficiency will boost productivity and customer satisfaction. Real-time monitoring, streamlining operations, integrating technology, and seamless communication and collaboration will take you miles ahead of your competitors.
All this and more is possible with the right software, which means saying goodbye to traditional tracking methods. Here is how you will benefit in the short and long run.
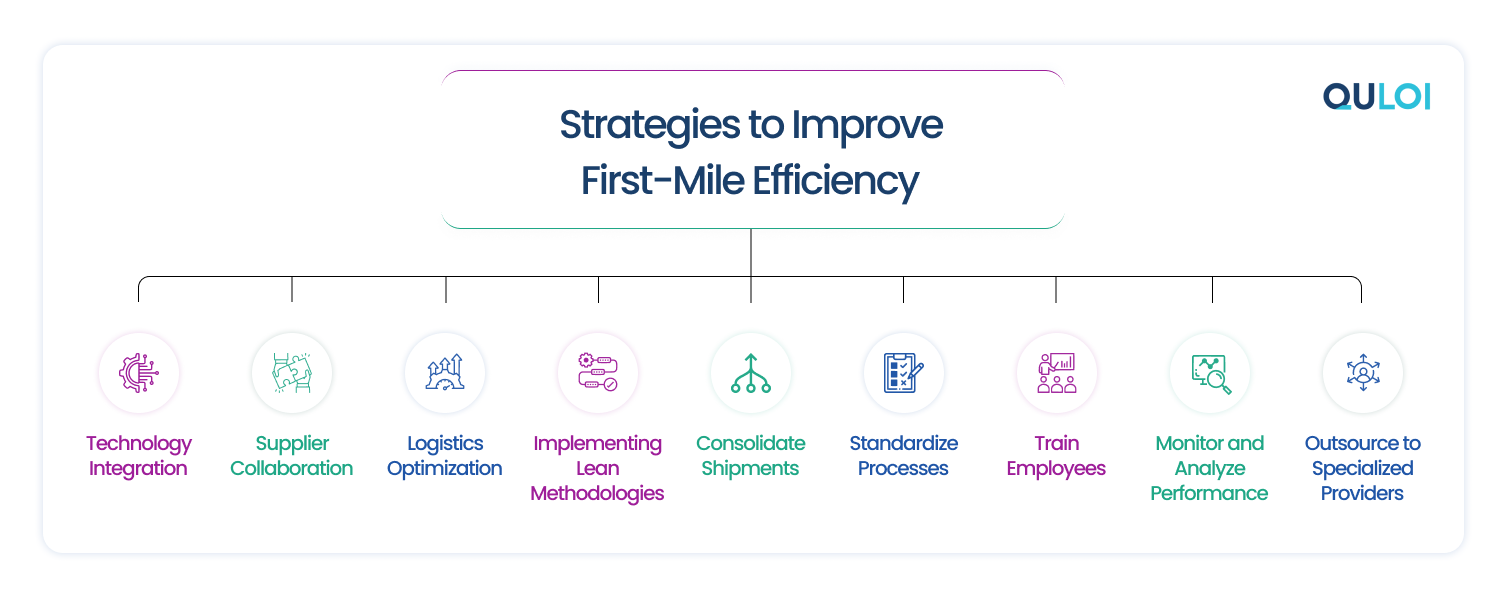
1. Technology Integration: Investing in transport management systems and automated GPS trackers will boost visibility and control. When you have access to the best routes and schedules, your employees will be pleased, and your customers will also thank you for delivering supplies on time. Even if they face issues, these tools will help you address them in real time, thus gaining customer trust and establishing long-term relations.
2. Supplier Collaboration: Understocking and overstocking are no less than a nightmare. Inventory management can be tricky if you are still relying on manual methods. With the right software, you can track and order items in advance. This will keep suppliers and customers happy, as they don’t need to deal with last-minute hassles.
3. Logistics Optimization: Finding the best routes with logistics optimization leads to reduced fuel consumption and lower emissions. Wait, there is more to it! You can adjust real-time schedules based on traffic, demand, and weather. Maximized vehicle capacity, automated dispatches, microwave housing, and crowdsourced delivery are benefits of optimizing logistics.
4. Implementing Lean Methodologies: Lean methodologies will help you identify waste and analyze areas of improvement. You will know precisely when to push out services/goods when needed rather than pushing them through the system. Moreover, error-free deliveries, maintained vehicles to reduce downtime, and regular improvement drives will make your processes seamless.
5. Consolidate Shipments: People from the same cities and localities often have bulk orders. You can combine packages into single shipments, reducing transport costs and boosting operational efficiency.
6. Standardize Processes: Another way to optimize first-mile deliveries is to have systems for pickups, sorting goods, and transportation that reduce errors. This will help you address issues faster, reduce waste, and significantly reduce costs.
7. Train Employees: Well, training is not limited to software and tools. You must ensure your drivers and logistics staff are well-equipped to handle customers. They will encounter a wide range of customers who may/ may not be pleasant. However, training them is your onus, which will help them develop their muscle in the long run.
8. Monitor and Analyze Performance: Tracking Key Performance Indicators (KPIs) is essential to transforming methodologies and keeping customers satisfied. You need to share your findings with your team, solicit input, and prepare an action plan.
9. Outsource to Specialized Providers: You might consider cutting costs by partnering with cheaper and inexperienced providers. However, hiring experts will help you adhere to deadlines and fulfill your customer commitments.
How Quloi Helps
1. Enhanced Visibility: With real-time order tracking and shipment visibility, you can be 1000% sure of your order deliveries. Not only will you be able to identify potential delays, but you will also be able to deal with issues proactively.
2. Streamlined Order Management: Quloi makes ordering a breeze with automated purchase order generation. The platform integrates seamlessly with ERP systems, ensuring data consistency and minimizing manual errors. Thus, you can safely eliminate errors and delays.
3. Supplier Collaboration: Managing suppliers, tracking performance, and establishing real-time communication can be challenging. However, the Quloin platform ensures a seamless response to requests, reduced delays, and a thorough supplier performance evaluation, ensuring reliable partnerships and smooth operations.
4. Actionable Notifications: When stakeholders receive proactive notifications and alerts based on predefined events, they can make faster decisions and address issues as they arise. This way, errors are sorted out in the first-mile delivery and don’t hamper the last stage.
5. Integration with Communication Tools: Communication is the backbone of the supply chain. Quloi integrates with tools like Microsoft and Slack, allowing instant messaging and file sharing with team members. This saves time switching between applications and boosts overall productivity.
If first-mile inefficiencies are a menace, it is time to bid them goodbye with Quloi.
Book a Demo to discover how to overcome them and stay miles ahead of your competitors.
Related Articles
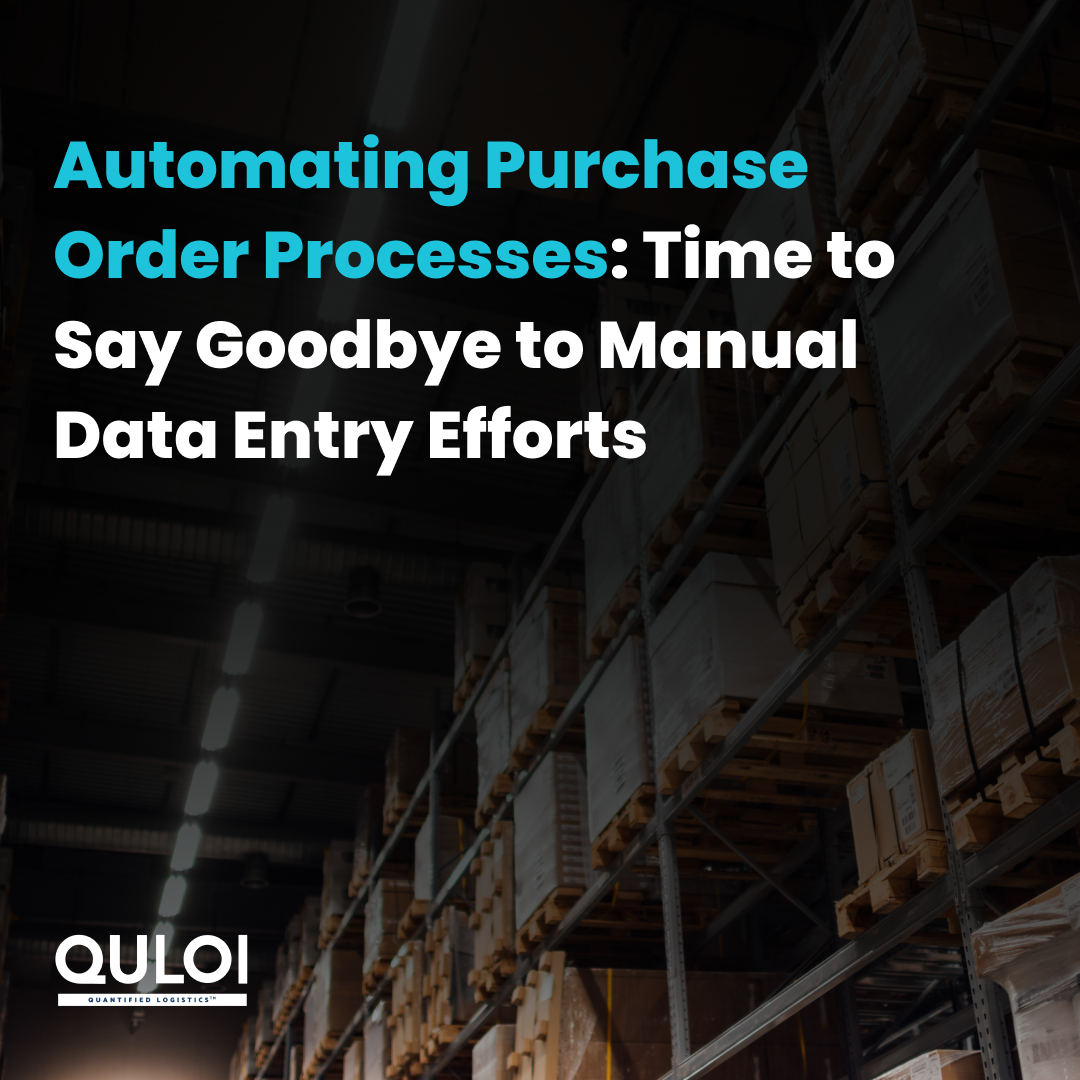
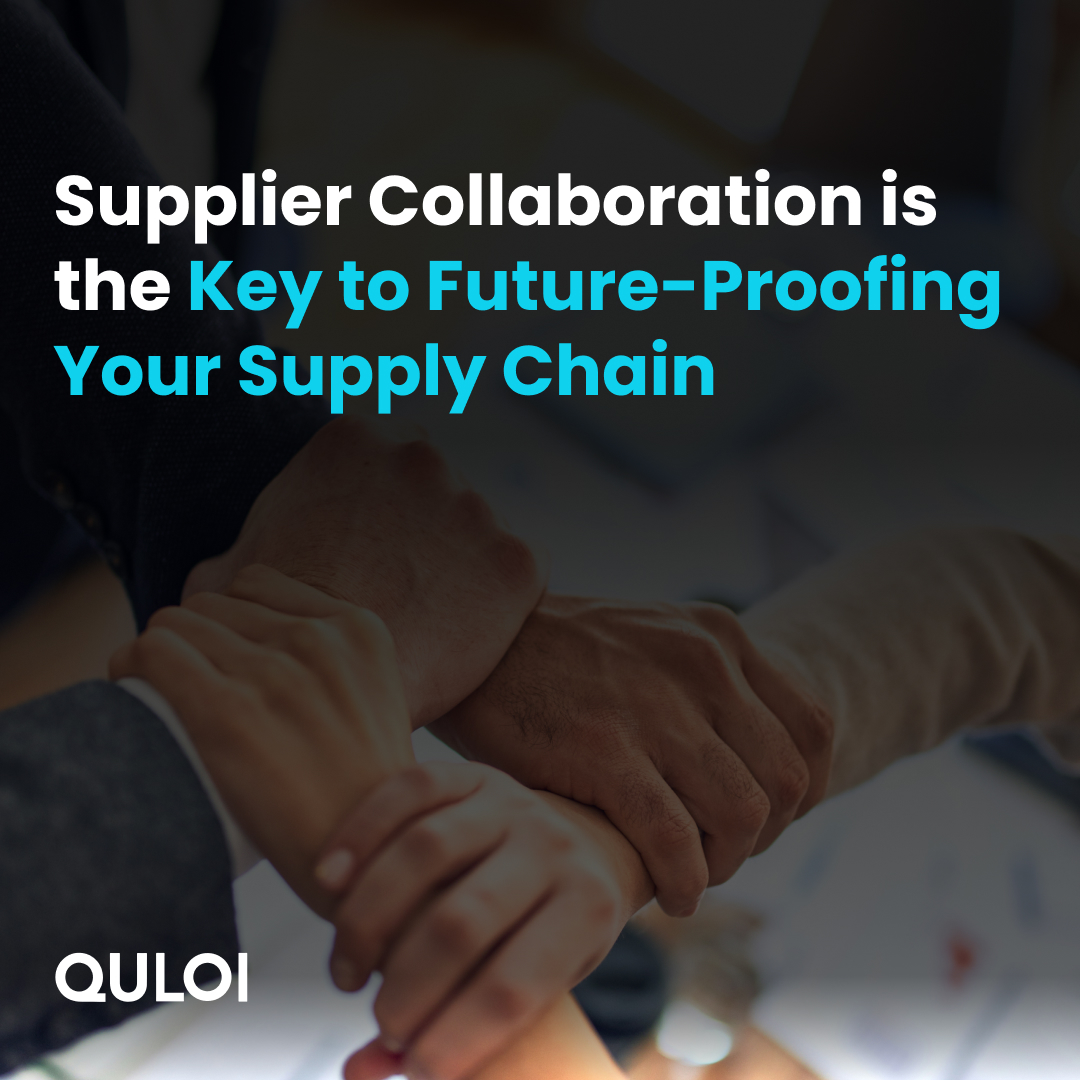
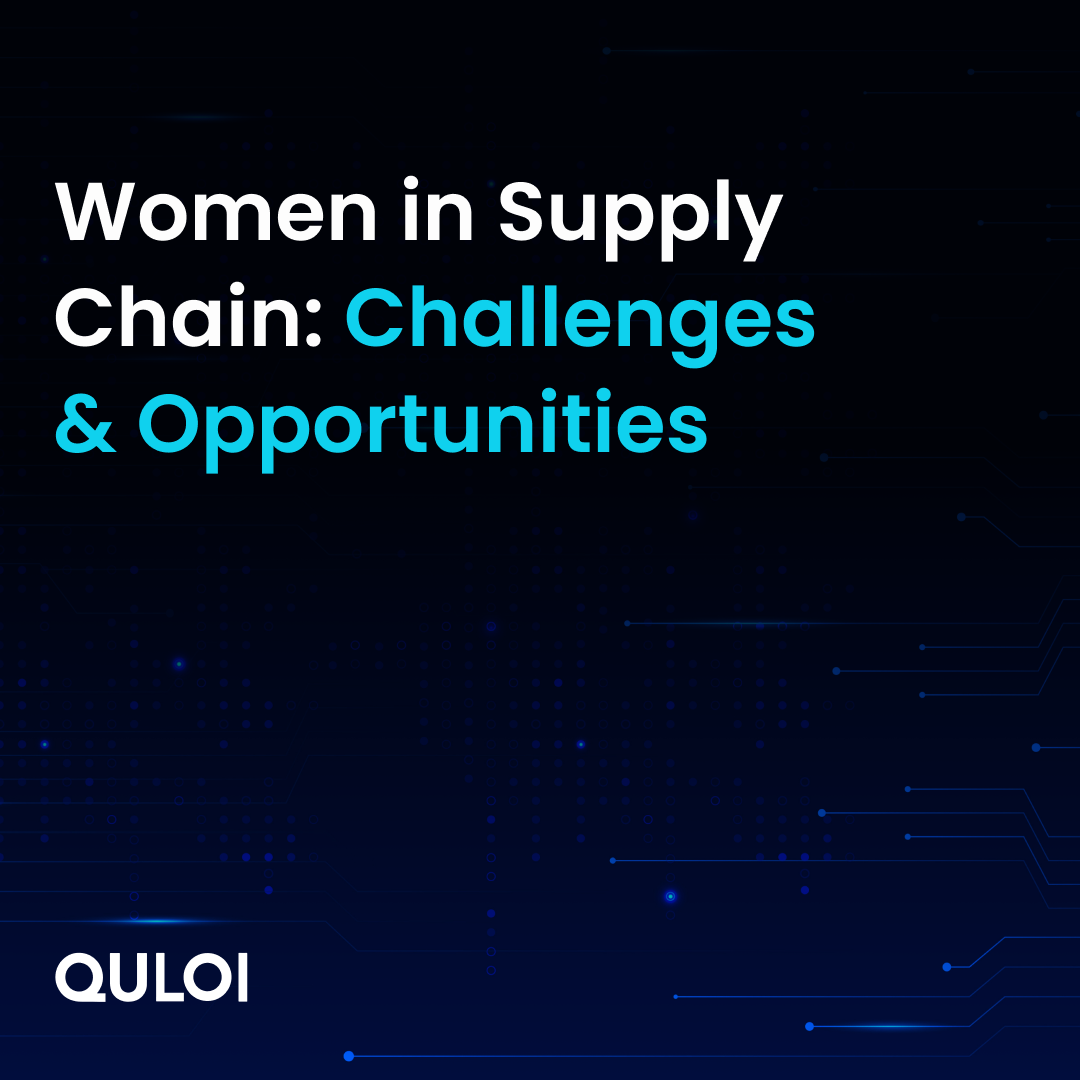