Best Practices to Avoid Detention & Demurrage Fees
It is often asserted that the major economic fallout in the last few years is that the era of globalization has passed. This notion is a myth.
If anything, forward-thinking leaders in the logistics industry spurred businesses worldwide to exploit growth opportunities in global trade while companies with outdated logistics processes lagged. In an era where customer expectations are lofty, time is valuable, and costs can quickly escalate, understanding the nuances of logistics and the detention and demurrage (D&D) charges that blindside us is crucial. Logistics is the backbone of global commerce, and Peter Drucker aptly stated, ‘What gets measured gets managed.’
But how do you measure what you want to measure?
An integrated and cost-effective global logistics sector is the fulcrum for such strategies. Logistics firms are under pressure to rapidly expand capacity, diversify routes, enhance network agility, and prevent D&D costs. The complexity of D&D costs is compounded by the multitude of parties involved – shipping lines, freight forwarders, terminals, and shippers—all of whom must navigate a landscape often lacking a centralized platform. This fragmentation makes it imperative for businesses engaged in global trade to understand their logistics processes well.
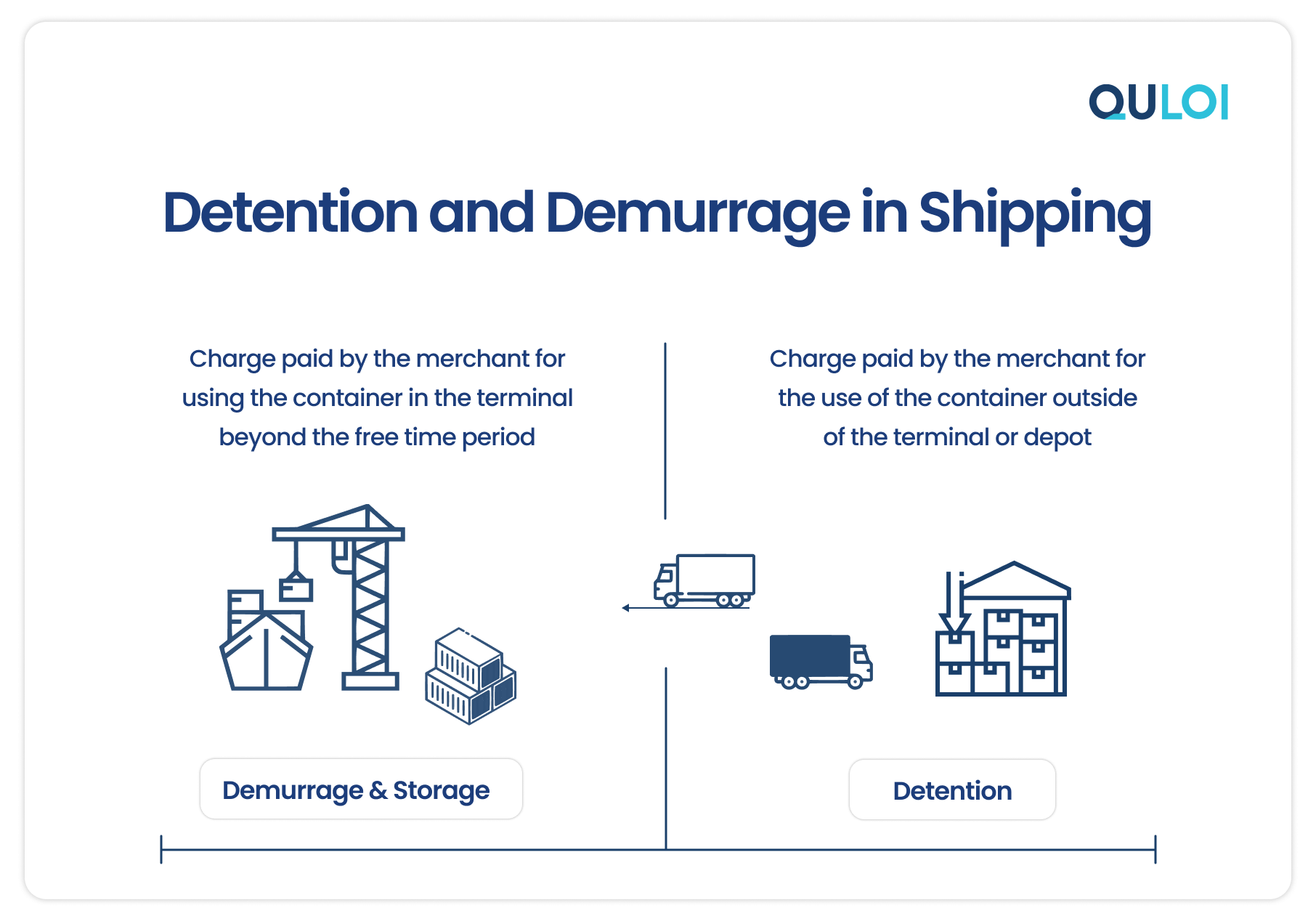
Are your current systems optimized for efficiency? Do you have clear communication channels with your logistics stakeholders?
Let’s dive into this blog to learn about effective strategies for preventing detention and demurrage charges and streamlining the shipping process with digital document management, real-time shipment visibility, and effective collaboration.
Causes of Demurrage and Detention Charges
D&D charges in the shipping industry represent more than just a line item on an invoice; they depict operational efficiency and strategic foresight. Let us discover the common causes of D&D charges that add quickly to your shipping.
Documentation Issues: Incomplete or inaccurate paperwork in shipping documents can prevent timely customs clearance. As a result, the cargo remains in the port’s custody until the consignee receives the necessary documentation on time. This space occupancy and additional costs result in demurrage and detention (D&D) charges. For example, the carrier can halt delivery upon a missing Bill of Lading (BOL), leading to unexpected costs for storage and handling.
Port Congestion: High port traffic means ships have to wait longer than usual to dock and unload their containers. In a recent event, during peak congestion at Singapore’s port in May 2024, containerships faced waiting times of up to seven days before they could berth. This means containers are held longer than the allotted free time at port. This inefficiency can cause shipping lines to impose demurrage charges on shippers. Also, increased cargo volume, inclement weather, limited terminal space, and other factors can all exacerbate the issue.
Customs Inspection and Clearance Delays: The complex customs clearance procedures remain a persistent issue. Extended inspections or issues with customs clearance can lead to containers being held longer than anticipated. According to the latest report, 4 billion paper-based documents are circulating in the trade system, with an inadequate degree of standardized information, systems, processes, and outdated laws. This increases the possibility of document errors that include bills of lading, bills of exchange, promissory notes, cargo insurance certificates, ship delivery orders, warehouse receipts, and more. This directly impacts the time containers remain idle and accrue D&D charges.
Cargo Abandonment: Research indicates that cargo is often considered abandoned in India if the consignee hasn’t claimed it for more than 30 days and up to 90 days in other countries. When a consignee fails to pick up their cargo or abandon it, it is held at the terminal for a prolonged duration, incurring demurrage fees for the shipper. Any dispute between shippers and consignees regarding cargo specifications or delivery terms (like missing licenses or rule changes) can lead to unavoidable delays and subsequent charges. For instance, if a consignee faces a demurrage charge of $140 per day for ten containers over a 7-day delay, they could have to pay a total charge of $9,800. When costs become unmanageable, importers may abandon their cargo in such cases.
Industry-wise Causes for Detention and Demurrage Charges
Understanding the unique challenges of specific industries is crucial to effectively managing D&D charges. Below, we explore the challenges and tailored solutions for the automotive, textiles, and electronics industries.
- Automotive Industry
The automotive industry is characterized by high-value shipments that require expedited handling. Delays at ports or during customs clearance can result in significant D&D charges, exacerbating costs for automotive manufacturers and impacting profitability.
How can automotive companies prevent D&D charges
Advanced Tracking Systems: Real-time tracking solutions allow stakeholders to monitor container statuses closely, enabling proactive management of potential delays.
Streamlined Customs Processes: Collaborating with experienced customs brokers ensures accurate and on-time documentation, minimizing the likelihood of customs-related delays.
JIT Inventory Management: With a just-in-time inventory approach, automotive companies can reduce the time their vehicles spend in transit and at terminals, thereby minimizing exposure to D&D charges.
- Textiles Industry
With seasonal demand fluctuations and perishable goods, the textile industry often requires swift customs clearance to avoid spoilage. Delays in customs processes mean increased D&D charges followed by financial losses.
How can textile companies prevent D&D charges
Temperature-Controlled Logistics: By investing in temperature-controlled transportation solutions, textile companies can ensure perishable textile products remain viable during transit, reducing spoilage risks while maintaining regulatory compliance.
Real-Time Customs Visibility: Leveraging software that provides real-time updates on customs clearance processes allows stakeholders to identify and address issues before they escalate into costly delays.
Efficient Documentation Management: Ensuring all necessary documentation is prepared in advance reduces the possibility of errors and information discrepancies that could lead to delays. Digital document management systems can help streamline this process.
- Electronics Industry
With consumers expecting immediate access to the latest technology and shorter product lifecycles, the electronics sector is experiencing rapid changes in consumer demand. Delays in shipping products can result in lost sales opportunities and ultimately increase costs due to D&D charges.
How can electronics companies prevent D&D charges
Agile Supply Chain Management: Develop a flexible supply chain that adapts quickly to market changes. This includes diversifying suppliers and using logistics partners who can respond rapidly to demand fluctuations.
Predictive Analytics: Data analytics tools help forecast demand accurately, allowing companies to adjust shipping schedules accordingly and avoid excess inventory at ports.
Collaboration Platforms: Implement real-time communication platforms that enhance communication among manufacturers, suppliers, and logistics providers, ensuring timely updates on shipment statuses and reducing delays.
Calculation of Demurrage and Detention Costs
Demurrage Calculation
Free Days: Most shipping lines offer specific free days (i.e., a grace period of 3 to 7 days) to pick up cargo.
Daily Rate: Once the free period/permitted time is over, demurrage charges apply, costing shippers $50 to $200 per day per container, depending on the shipping line and location.
For example, if a container incurs a demurrage charge of $150 per day after a 6-day free period and it remains unpicked/unclaimed for an additional 10 days:
Total Demurrage Cost = Daily Rate × Days Overdue = 150 × 10 = $1, 500
Detention Calculation
Free Days: Similar to demurrage, free days are usually allowed for returning shipping containers.
Daily Rate: Detention rates vary widely but typically range from $75 to $150 per shipping container per day.
For example, If a container is detained for 5 days beyond the permitted time at a rate of $130 per day:
Total Detention Cost = 130 × 5= $ 650
Best Practices to Prevent Demurrage and Detention Charges
Optimize Container Pickup Scheduling: Coordinate with logistics providers to ensure all relevant documentation and arrangements are in place before the cargo arrives. This proactive approach ensures containers are collected on time, minimizing the likelihood of incurring demurrage fees.
Leverage Container Management Software: Use container management solutions to track container usage, availability, and return schedules. This helps companies enable proactive returns when containers reach their free time limits. The image below shows detailed information for each container in the shipment.
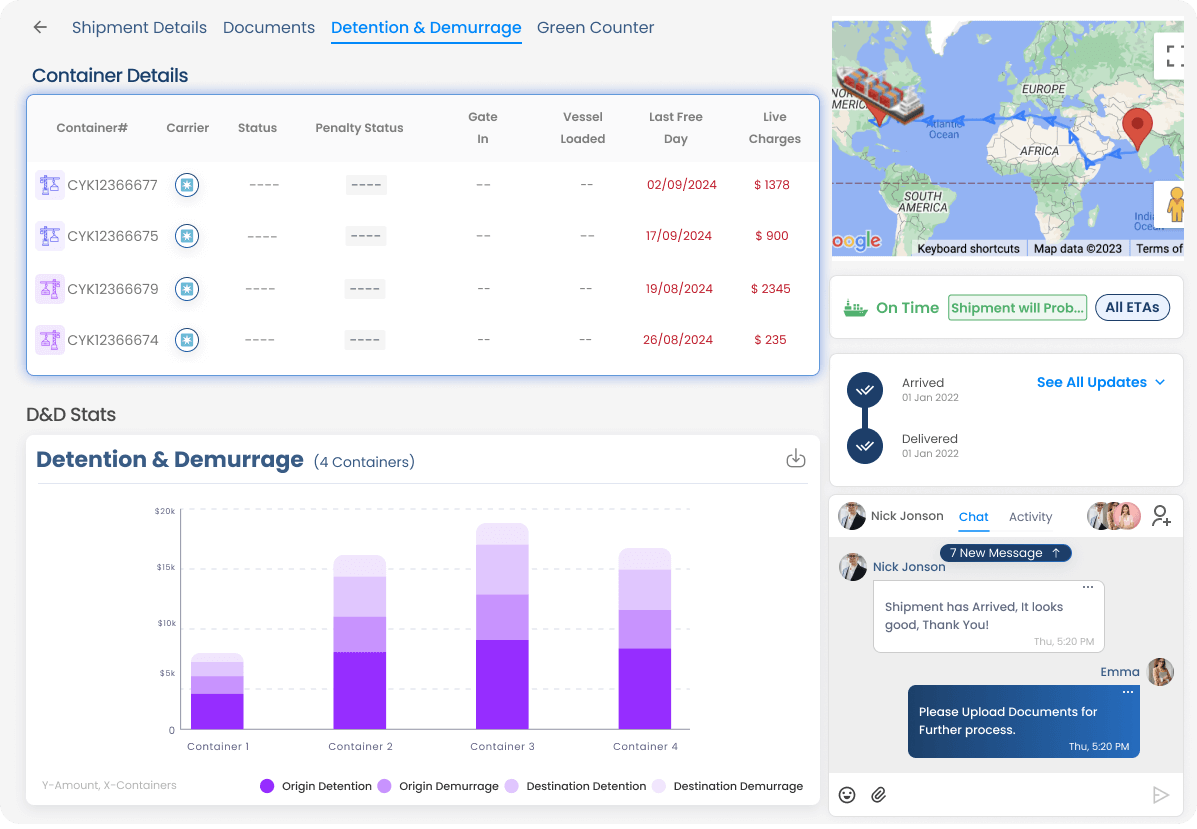
Improve Documentation Accuracy: Implement a checklist for all necessary documents (e.g., bill of lading, shipping invoice, customs paperwork) before the cargo arrives. Leverage digital document management systems to ensure all paperwork is accurate and readily available, speeding up customs clearance and reducing delays.
Implement Real-Time Tracking Systems: Utilize GPS and RFID technology to determine the current location of containers in real time. This real-time visibility allows logistics managers to constantly monitor container locations, identify potential delays early, and make necessary adjustments.
Establish Strong Relationships with Customs Brokers: Collaborate and work closely with customs brokers who understand the nuances of local regulations. This will ensure swift clearance and minimize the risk of detention fees due to prolonged customs processes.
Negotiate Free Time Extensions: Based on your shipping patterns, negotiate longer free periods for demurrage and detention charges with your carriers. This can help hold your cargo beyond the agreed time and help you reduce the risk of unexpected feeds during peak seasons.
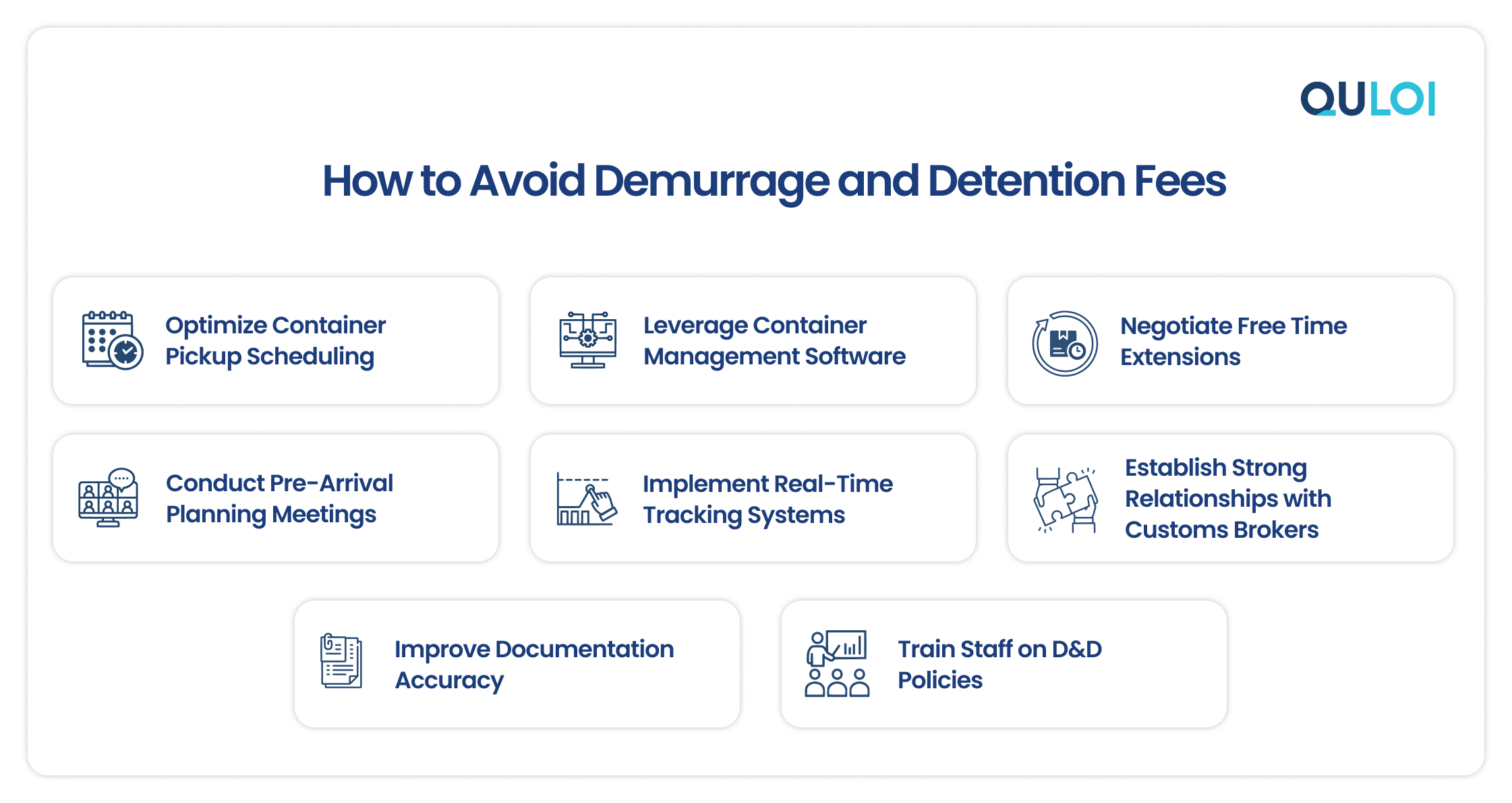
Conduct Pre-Arrival Planning Meetings: Regularly plan meetings with your logistics stakeholders (freight forwarders, suppliers, transport companies) to align your shipping expectations and responsibilities.
Train Staff on D&D Policies: The best way to reduce D&D charges is to understand the financial implications of delays. Stay informed about the freight market conditions, daily rates, and specific contract terms. This information lets you anticipate fluctuations and negotiate better terms with service providers and carriers.
Recent Regulatory Developments
In February 2024, the FMC introduced new regulations aimed at improving transparency and fairness in demurrage & detention billing practices. These regulations state that:
- Billing Eligibility: Demurrage and detention invoices can only be issued to the party contracting for cargo transportation or storage. Thai ensures accountability and prevents multiple parties from being billed simultaneously.
- Billing Timeframe: Common carriers are required to issue D&D invoices within 30 days of the charge’s occurrence. This provision promotes timely communication and helps reduce billing disputes.
These regulatory changes are designed to protect shippers from unfair penalties due to port congestion, customs delays, or other factors beyond their control. The FMC’s Interpretive Rule clarifies that D&D charges should not be applied when shippers have reasonably tried to retrieve their cargo but are delayed by service disruptions or unforeseen external factors.
Every Dollar Counts: Save on D&D Charges with Quloi
The high costs related to the time containers spend at ports have been an area of friction for logistics companies, and they continue to be so. Unfortunately, many logistic companies are held back by outdated IT infrastructures, fleet management, and warehousing systems, which affect their ability to innovate fast enough to differentiate better. Also, as environmental and sustainability concerns arise, the need for real-time data to navigate and leverage additional charges and stay compliant has become important. Every dollar counts, and with outdated systems and processes – logistics stakeholders are forming a ground that incurs detention and demurrage charges. Why let your hard-earned profits slip away when you can leverage the Quloi platform to streamline your shipping process!
A robust solution facilitates seamless data exchange among shippers, freight forwarders, customs brokers, and other key players, ensuring real-time access to shipment details and documentation in multiple languages for cross-border trade. Centralized workspaces streamline collaboration by making sharing essential documents and updates easy without wasting time searching for information. With real-time visibility into customs clearance activities, Quloi ensures stakeholders proactively track shipments, address potential issues before they escalate into D&D charges, and foster an equitable environment for all stakeholders. Integrated communication tools enhance interaction among all parties involved, while automation of workflows improves overall efficiency in customs processes. Secure audit trails provide quick access to historical data for informed decision-making.
The race is on for smart, superior, and streamlined logistics. Is your organization ready?
Book a Demo to get started today
Related Articles
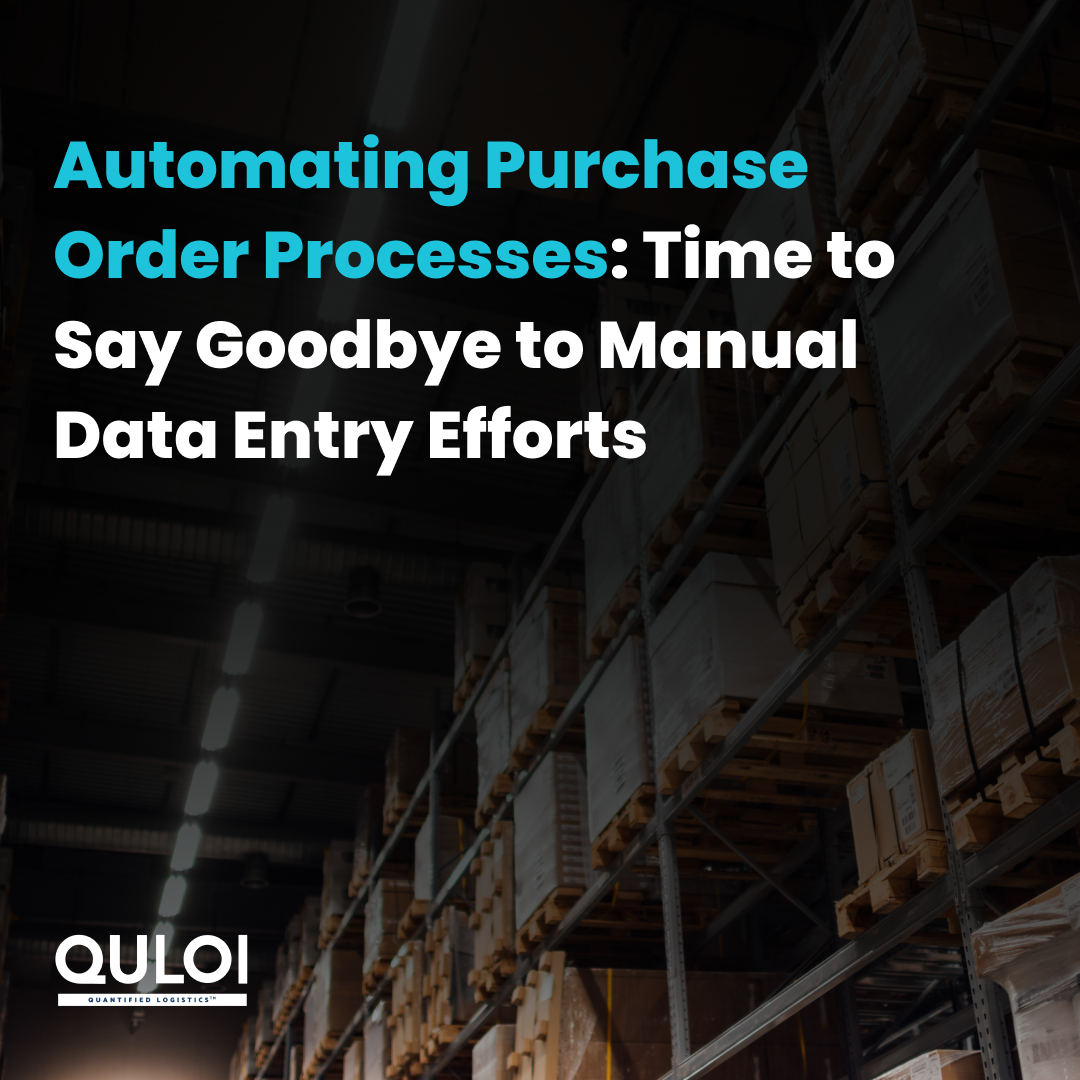
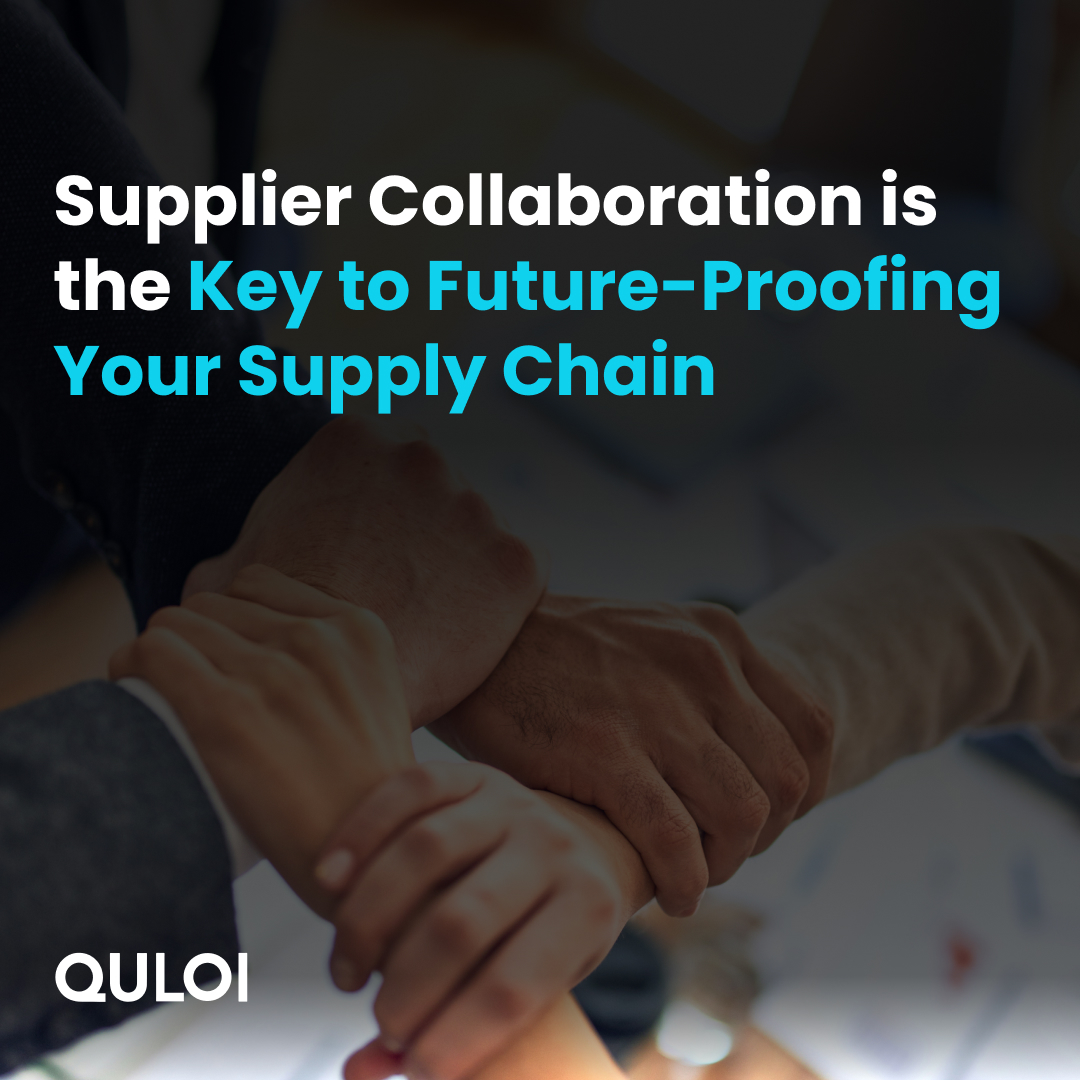
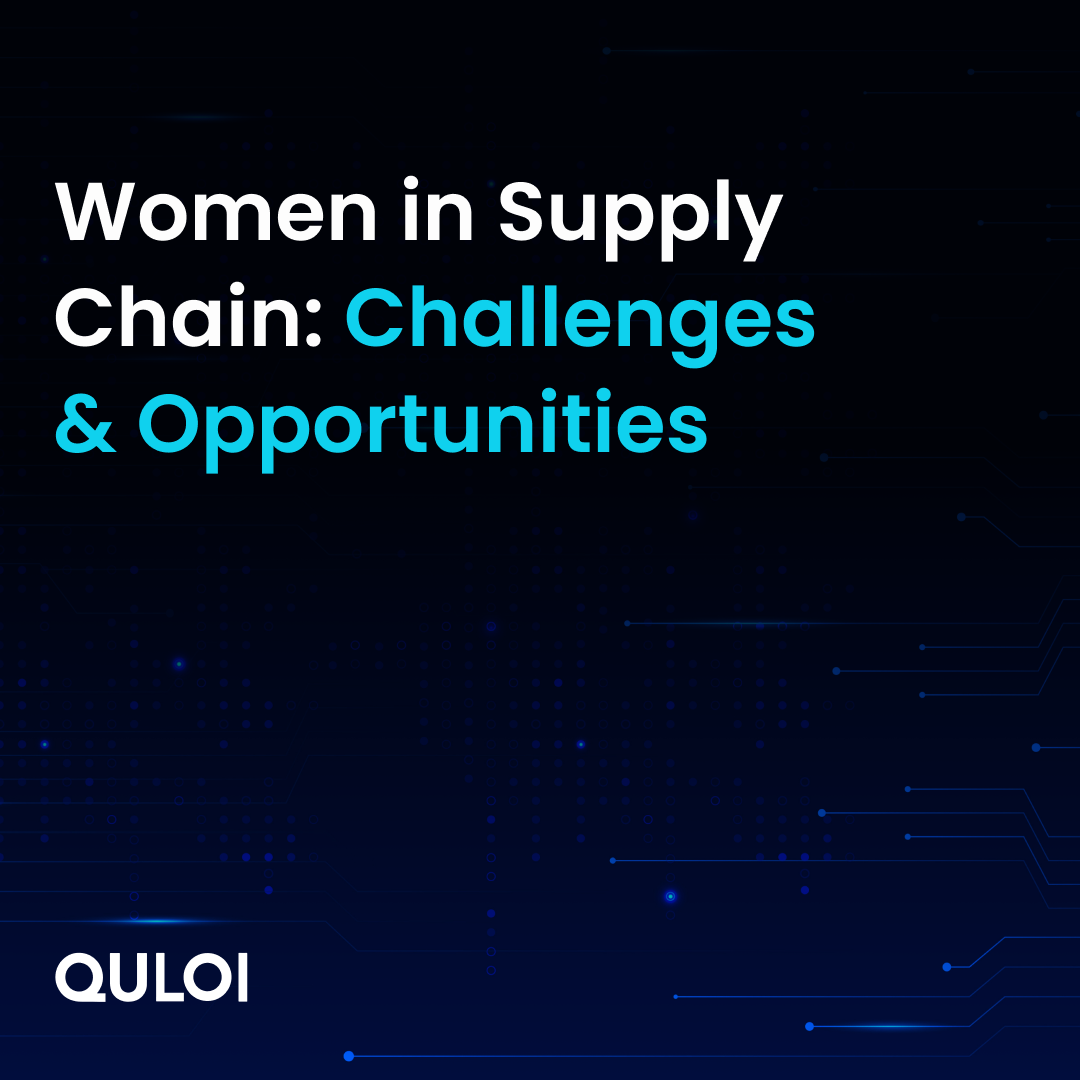