Trump Tariff Tsunami: Impact and Measures
The global trade landscape has been prone to turbulence. Still, the imposition of steep tariffs by the U.S., EU, China, and other major economies remains a top concern for many executives. From automotive hubs in Japan to pharmaceutical leaders in India, nations have long thrived on production processes that fuel the global economy. The looming tariff tsunami has sent shockwaves through global supply chains and logistics. As manufacturers feel the heat, businesses face a stark choice– absorb the sweeping tariff costs or pass them on to their customers. The concern is no longer if logistics operations will be disrupted, but how intensely and for how long.
Those who understand tariffs and their likely impacts will be better positioned to mitigate the potential effects of tariffs and implement risk mitigation strategies. This blog examines the latest trends in global tariffs, their direct and indirect impact on supply chains and logistics, and the measures that CFOs and CEOs can consider to mitigate supply chain risks and capitalize on potential opportunities.
The Current State of Global Tariffs
Tariffs have long been a contentious aspect in the global trade environment, imposed by governments primarily for these reasons: to boost domestic production, address trade imbalances, or exert geopolitical pressure. However, tariffs introduce significant financial and operational complexities.
United States’ Aggressive Tariff Escalation: The Trump administration dramatically increased tariffs, imposing a 125% ad valorem duty on Chinese imports. This new tariff was added to existing levies, including a 20% national security tariff and sector-specific duties, with some technology products facing tariffs ranging from 7.5% to 25%. Beyond China, the White House cited reciprocal tariffs on more than 15 countries, including India, Brazil, and Germany, with rates as high as 50%. These tariffs are measured based on trade deficits and non-tariff barriers. Additionally, a blanket 10% tariff applies to nearly all imports, with exemptions for critical necessities, including food, medicine, and strategic minerals. The US also revoked duty-free de minimis privileges for Chinese e-commerce shipments, increasing the cost of small-scale imports. US Customs provided some transitional leeway to importers by allowing the application of previous tariff rates on goods that entered Foreign Trade Zones before March 12, 2025.
International Organizations’ Assessments: The World Trade Organization (WTO) revised its global trade growth forecast, slashing it by 1.5% for 2025. This revision cites tariff-induced trade diversion and ongoing supply chain disruptions. Meanwhile, the United Nations Conference on Trade and Development (UNCTAD) raised concerns about the increased vulnerability of developing countries, projecting a 0.7% GDP contraction for several export-reliant economies due to reduced market access and fragmented global value chains.
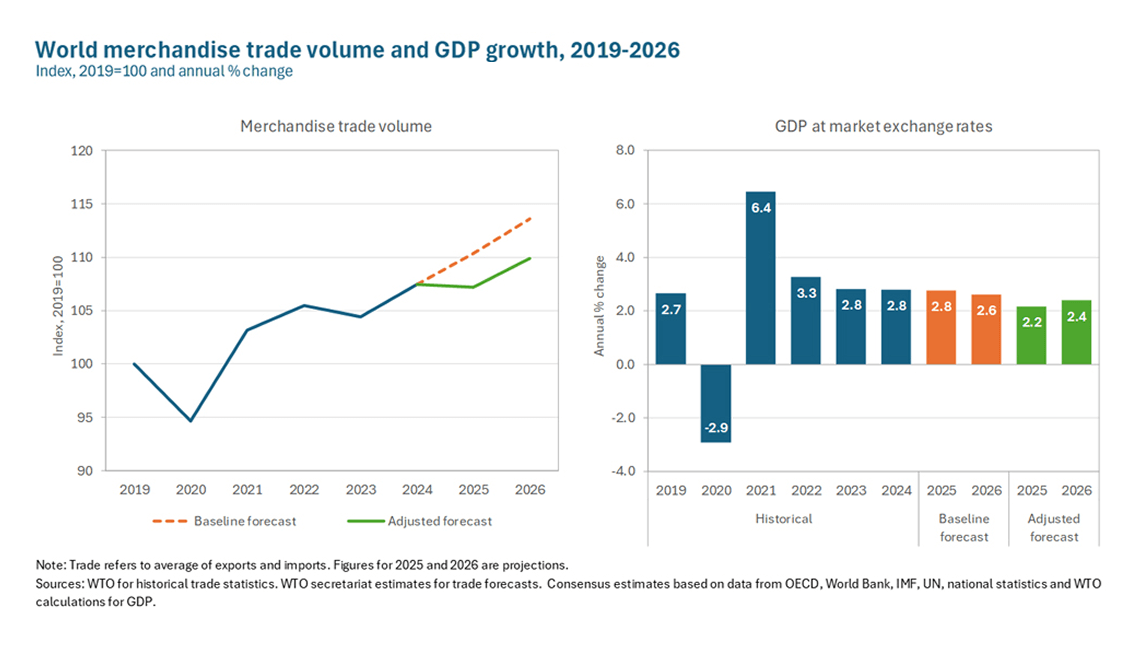
China’s Retaliation and Economic Measures: In response to U.S. tariffs, China responded swiftly with a 125% levy on American goods, targeting agricultural exports and high-tech components. This aggressive escalation has expedited the unwinding of US-China supply chains. Projections by Oxford Economics suggest bilateral trade could contract by as much as 80% if the conflict persists. China devalued the yuan by 2.3% to mitigate its economic impact, potentially sparking a currency war and exacerbating market instability. The Chinese government also announced a $220 billion stimulus package to subsidize exporters and support affected industries. However, this move has increased the national fiscal deficit to 5.8% of GDP, raising concerns about the country’s long-term economic sustainability.
European Union’s Strategic Pause and Preparedness: The European Union has paused its planned retaliatory tariffs against the US for 90 days, offering a negotiation window. Still, if negotiations fail, it is fully prepared to impose duties of up to 20% on $45 billion in U.S. goods, particularly agricultural products and digital services. This strategic pause enables the EU to achieve its dual objective of striking a balance between industry protection and diplomatic engagement. Simultaneously, the EU is rapidly expanding trade diversification with ASEAN and Mercosur partners to reduce its dependence on American and Chinese markets.
Who’s Affected: Regional and Sectoral Impact
The 2025 tariff escalations are being felt across global industries, with certain US regions facing acute challenges than others. In the US, the manufacturing strongholds of Michigan, Ohio, and Indiana bear the heat of tariffs. The automotive industry, which relies heavily on cross-border supply chains involving Canada and Mexico, has an effective tax rate of 17% on imported parts and components. This steep taxation is likely to reduce competitiveness, increase production costs, and potentially put manufacturing jobs at risk. Additionally, consumer prices are poised to rise, with new tariffs on Chinese electronics and European machinery estimated to be between 1.2% and 2.5% annually.
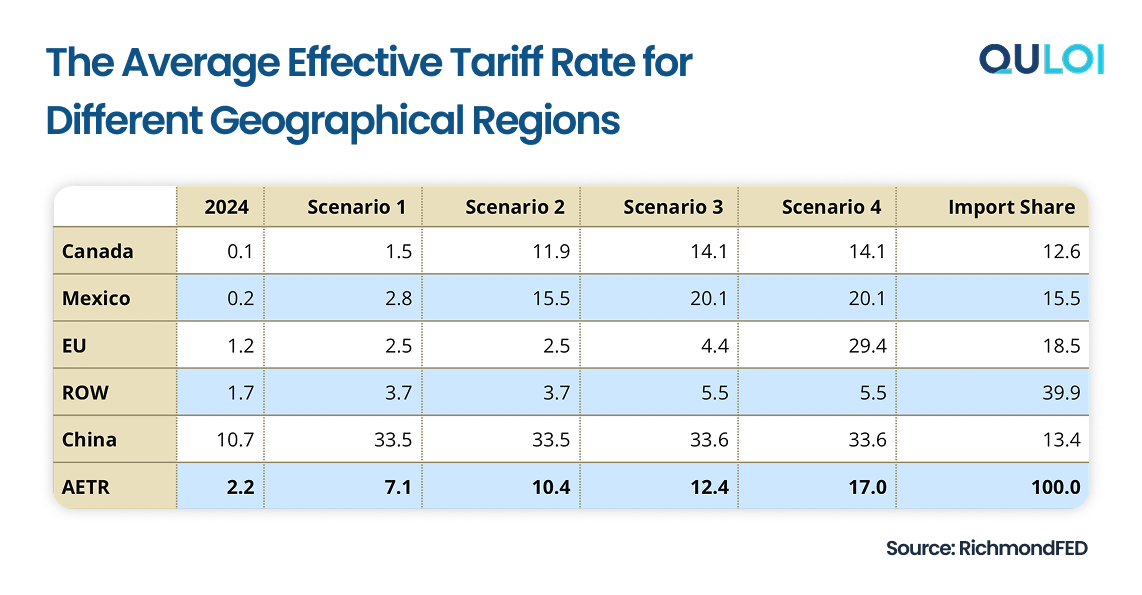
China’s export sector is facing a sharp contraction, with second-quarter 2025 exports indicating a 12% decline. This contraction risks losing approximately 3.1 million manufacturing jobs, thereby intensifying economic and social tensions. The Chinese government introduced a substantial stimulus package to mitigate these impacts. However, the increased fiscal deficit of 5.8% has sparked concerns regarding long-term economic stability.
Targeted US tariffs are severely impacting EU powerhouses France and Germany. French wine producers, with €2.3 billion in exports, face significant headwinds. Germany’s €18 billion auto parts export sector is vulnerable to US tariffs, posing a threat to a key industrial sector. In a strategic pivot, intra-EU trade in machinery has increased by 14%, as companies aim to mitigate external tariff risks by reshoring production within the bloc. This move will help reduce overall efficiency and increase costs.
Tariff-driven disruptions are hitting developing economies the hardest. Sub-Saharan Africa, which heavily relies on exporting raw materials to China, may experience a potential decline of $14 billion in export revenues. Meanwhile, Southeast Asian nations, such as Vietnam, are bracing for an 8% decline in electronics manufacturing output due to spillover effects from US tariffs on Chinese components. The consequences go beyond trade, undermining progress in poverty reduction and destabilizing fragile economies.
Tariff pressures are influencing global industries in different ways. The U.S. auto sector is under strain, with new duties on Mexican auto parts disrupting $30 billion in trade and leaving about 45,000 assembly line workers vulnerable to layoffs. Meanwhile, electronics giants like Apple are facing reported component cost increases of 12–15% as tariffs impact semiconductor prices. On the agricultural front, Brazil’s soybean exporters benefit from shifting trade dynamics, with shipments to China increasing by 22%. Unfortunately, US farmers face setbacks, reporting a $4.6 billion decline in export sales.
In response to such challenges, many corporations are taking preemptive and protective measures to mitigate risks in their supply chain for the future. Surveys indicate that 53% of manufacturers have accelerated their nearshoring strategies, with Mexico and India set to benefit primarily. Companies are considering reclassification of products under distinct Harmonized System (HS) codes to exploit tariff loopholes, promising a 9-14% duty reduction.
What CFOs and CEOs Must Know in 2025
With more tariffs, executive orders, and austerity measures on the horizon, it is imperative for CEOs, CFOs, and decision makers to address uncertainties, withstand supply chain disruptions, and maintain operational resilience. Based on industry analyses, here are a few critical strategies that CFOs and CEOs can consider:
1. Risk Assessment and Scenario Planning
It is critical to map supply chains beyond immediate suppliers to spot hidden vulnerabilities. CFOs must evaluate the performance of second- and third-tier (raw material suppliers) to identify potential tariff exposures. For example, Cracker Barrel identified that 33% of its retail products imported from China faced tariff risks, impacting 20% of its revenue. Thorough multi-tier supply chain audits, such as reclassifying goods under the Harmonized Tariff Schedule (HTS) codes, ensure risk mitigation.
Conduct scenario analysis ranging from moderate tariff surges to worst-case escalations. Gartner reports that 74% of chief supply chain officers (CSCOs) view tariffs as a catalyst for strategic shifts in their organizations. CSCOs should develop financial models that account for negotiating with suppliers, leveraging currency fluctuations, and aligning with leadership on cost strategies.
2. Supply Chain Diversification
65% of CFOs consider negotiating with suppliers to manage tariff costs, while 48% explore alternative sourcing in new markets and low-tariff geographies. For instance, organizations are diversifying their pharmaceutical sourcing beyond India and relocating semiconductor production from Taiwan to the US.
Optimize product designs to reduce tariff deficits. Leverage tariff engineering strategies like free trade zones and adjusting country-of-origin destinations.
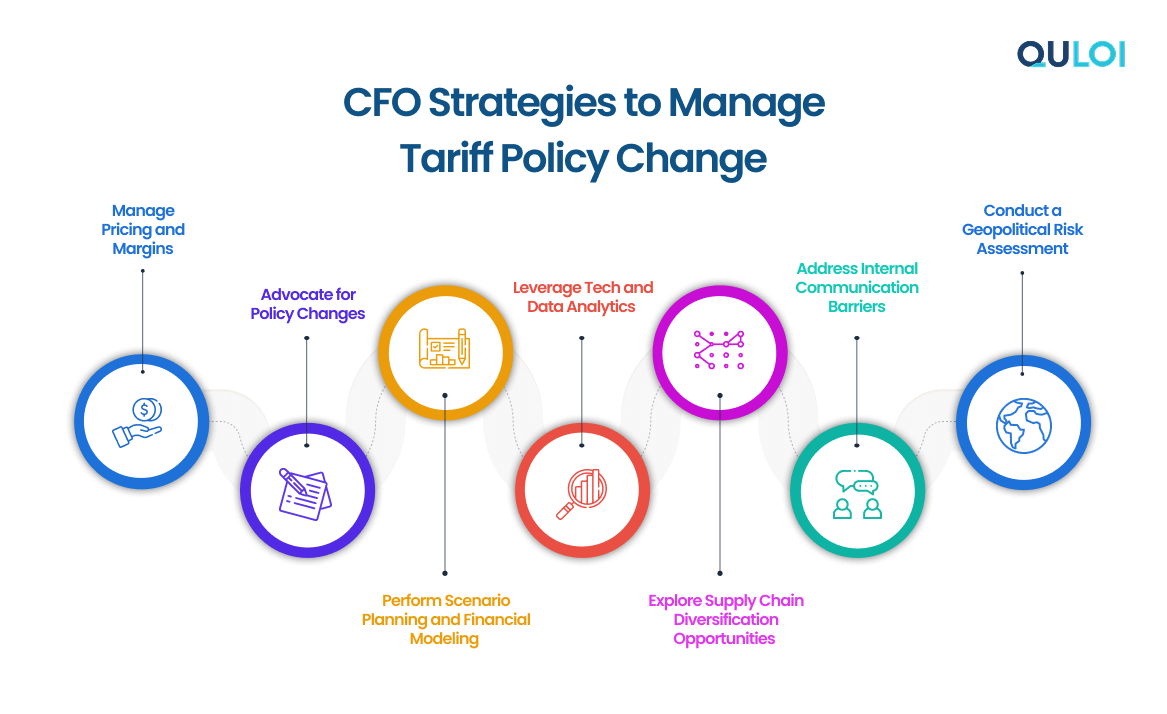
3. Pricing and Margin Management
CFOs should consider implementing AI-powered tools to enable dynamic pricing strategies in real time for monitoring peer performance. A Gartner study found that 45% of CFOs are passing tariff costs on to consumers, although visibility and transparency are crucial for retaining consumer trust.
4. Technology and Data Utilization
Implement AI-based tools for inventory optimization, demand forecasting, and waste management to enhance operational efficiency and effectiveness. Scheider Downs, a US-based accounting firm, highlights the importance of agile pricing models powered by real-time data.
Smart tracking systems help reduce customs delays by identifying inefficiencies and automating tariff classifications. Quloi provides real-time visibility into customs clearance activities by ensuring stakeholders proactively track shipments and address potential issues before they escalate into demurrage and detention (D&D) charges.
5. C-Suite Collaboration
CFOs must coordinate with CEOs, CSCOs, and board members to strike a balance between cost, risk, and resilience. Gartner emphasizes storytelling techniques to communicate data-driven insights and the data to align leadership on tariff exposures and response strategies. Allocate contingency reserves to manage tariff volatility, including safety stock and alternative logistics routes, ensuring a stable supply chain.
6. Policy Advocacy and Compliance
Industry groups must advocate for tariff exemptions or phased implementations. CEOs and CFOs must prioritize regularly auditing HTS classifications and reviewing transfer pricing structures to reduce the risk of penalties and maximize duty savings.
Concluding Note
Tariffs are expected to continue reshaping and influencing global supply chains in 2025, prompting businesses to adapt to compliance optimization, increased agility, diversification, and advanced risk management. While these tariffs present challenges, Quloi empowers organizations to stay innovative and competitive by enabling smoother supplier onboarding and multi-tier collaboration.
To learn more about navigating an ever-evolving trade environment, book a FREE demo with Quloi.